Microwave Components
An industrial microwave is made up of three basic components. A generator or transmitter, waveguide and an applicator.
Generator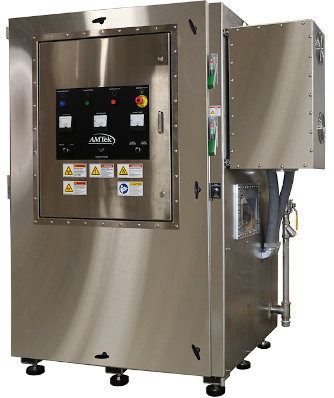
The generator or transmitter is the heart of the system. Its main purpose is to convert electric line power to microwave energy. A traditional microwave generator is primarily made up of a solenoid, a magnetron tube and a transformer. The transformer is used to create the high voltage necessary, the magnetron tube is what emits the microwaves, and the solenoid which is wrapped around the magnetron tube creates a magnetic field to regulate the power of the microwaves produced. These components are housed in a stainless steel enclosure that is temperature controlled. A solid-state transmitter uses lower voltage, DC electricity and multiple transistors to produce microwaves. Each transmitter can generate 50, 75 or 100 kW of microwave energy and is precisely controllable via the operator touchscreen or computer interface.
Waveguide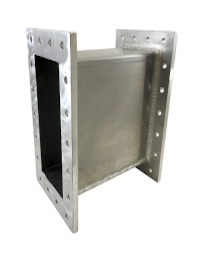
The next component that makes up industrial microwaves is the waveguide. It is the simplest component of the system and as its name implies, it guides the microwaves from the transmitter to the applicator. The waveguide is usually made out of aluminum to reduce weight. The dimensions of the waveguide allow microwaves to resonate through the waveguide with virtually no loss. These waveguides can go long distances and carry microwaves from one part of your facility to another. This is advantageous if you are limited on space or want to isolate your transmitters from heat, dirt, moisture, etc. These waveguides are very similar to coaxial cable or AC power lines. Waveguide is also used in the radio and radar industries, not just industrial microwaves.
Applicator
The destination for the microwaves is the applicator. This is where the microwave energy meets the load. There are many types of applicators available including:
- Ovens, both batch and continuous that can be configured to have multiple air intakes and exhaust ports, microwave safe doors, and conveyor belts.
- Vertical tanks that have very uniform heating properties and make great replacements to conventional steam jacketed tanks and heating vessels.
- Horizontal mixers that can be advantageous when continual mixing and conveying is required, but the material is not suited for pumping.
- Your brain child! We know that not all products or processes work in the off-the-shelf applicators and we are continually advancing new industrial microwave applications and applicators.